Beamo Use Case for Digital Transformation in a Steel Factory: SeAH Changwon Special Steel (SeAH CSS)
- Leveraging a fast, easy, and cost-effective solution for implementing digital twins, SeAH CSS aims to extend the deployment across its 9 factories and 3 additional sites.
- Real-time machine data monitoring and maintenance within the digital twin.
- The solution facilitate seamless self-onboarding and remote training, particularly enhancing education on hazardous and restricted areas and promotes collaboration across SeAH's extensive facility network.
- Documentation of worksite conditions and protocols for compliance with health and safety regulations.
SeAH Changwon Special Steel (SeAH CSS) is a specialized company established in 1966, producing advanced industrial steel materials and high-value special alloys for the aerospace, defense, and aviation industries.
SeAH aims to implement a digital factory in the digital realm, allowing engineers to access real-time information, such as equipment performance, without the need to visit the site in person.
The long, hard journey towards
complete digital transformation
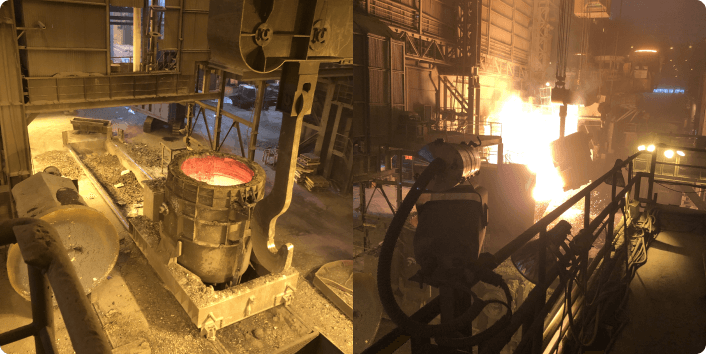
Established in 1966, SeAH Changwon Special Steel is a specialized company producing advanced industrial steel and high-value special alloys for the aerospace and defense industries. As a leading player in the specialty steel industry, SeAH has long been driving digital transformation across its organization.
Operating nine factories, with the smallest one spanning 23,500m², each facility utilizes an average of four production lines and advanced equipment. To prevent production delays, meticulous maintenance and monitoring by factory personnel are crucial. Inspecting a single facility requires manually collecting up to 7,000 photos and videos over several months. The time-consuming process extends to organizing and reporting, rendering the collected data obsolete after reporting.
Additionally, manual inspection of machinery posed safety risks, especially in the harsh conditions of the steelmaking process. With 30-40 machines operating simultaneously in a single factory, engineers couldn't sample internal conditions without stopping the machines, due to the inability to lift covers during operation.
SeAH Changwon Special Steel aimed to implement the conditions and situations of the physical world into a virtual space for safer and more efficient equipment monitoring and maintenance. Choi Min-seok, Executive Vice President and Head of R&D, explored various solutions, including CAD, to replicate the factory into a virtual version. However, creating a digital twin for just one factory involved eight employees and took seven months. The resulting 3D virtual space, completed over seven months, was an 8 minutes video, proved challenging to use effectively, as integrating real-time data feeds into the digital twin was unsuccessful.
Moreover, SeAH faced a significant setback in its digital transformation plan as it struggled to connect its in-house platform, Data Forge, which automated processes using robot arms and sensors within machinery, to the digitally replicated factory.
A faster and simpler way to make digital twins
SeAH and Beamo embarked on the proof-of-concept (POC) for implementing a digital twin on the Small Rolling Mill (RSB) machine. Utilizing Beamo, SeAH Changwon Special Steel swiftly implemented a 360-degree view of the expansive factory and established a real-time monitoring system. Now, inspectors can capture challenging areas such as dark corridors, underground spaces, and the interiors of heavy machinery using Beamo, enabling them to view the machine's interior within the digital twin platform from anywhere at any time.
Engineers at SeAH were impressed by the speed at which Beamo enabled the implementation of the digital twin. "Compared to several months required by previous solutions, Beamo allowed them to create a digital twin in just a few hours, significantly reducing the time spent while delivering excellent results."
To overcome the challenges of dark factory conditions, Beamo introduced a new feature allowing users to preview 360-degree photos before capture. Additionally, users could modify camera settings (ISO sensitivity, HDR, shutter speed, etc.) through the Beamo app as needed.
Upon completion of the digital twin with 360-degree views, SeAH utilized tagging features to upload safety guidelines and educational materials, facilitating safety management for employees. Integrating sensor data from rolling machines allowed engineers to monitor immersive information based on spatial data.
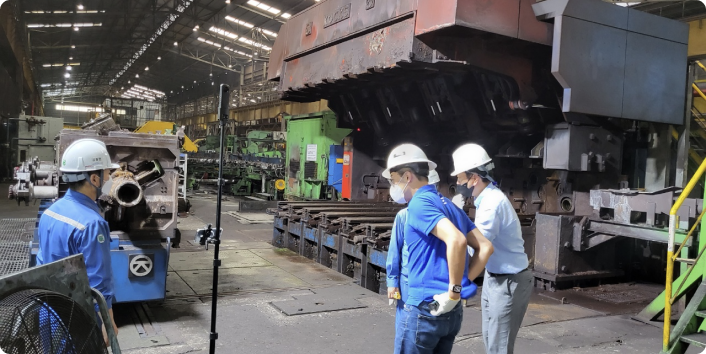
Beamo integrates with SeAH's Data Forge, displaying RSB data charts through Tag. Engineers can now assess issues without the need for on-site visits, gaining insights into the situation within the digital twin.
Prepare for Expansion
Now, engineers can remotely monitor real-time data within the digital twin without visiting the site, enabling them to collect and utilize various information remotely. Real-time machine monitoring allows immediate identification of issues in specific areas or equipment within the digital twin, enabling prompt actions.
SeAH also digitized employee safety training using the digital twin. Navigating the entire factory to onboard employees in the expansive and complex facility was challenging. However, after Beamo's implementation, employees could virtually experience the factory within the digital twin platform, facilitating self-onboarding. Moreover, it was utilized for regular safety training for employees in a factory with many hazardous devices and restricted areas.
Thanks to easy capture methods, rapid post-processing, and a cost-effective solution, SeAH efficiently digitized its 23,500m² factory in a short period. The company plans to expand the application of this solution to the remaining nine SeAH CSS factories (each with 30-40 machines) and three additional sites.