디지털 트랜스포메이션을 위한 철강 공장의 Beamo 도입 사례
: 세아창원특수강(SeAH CSS)
- 디지털 트윈을 빠르고 쉽게 비용 효율적으로 구현할 수 있는 솔루션을 바탕으로 SeAH CSS의 9개 공장을 비롯한 그 외의 3개 현장까지 확장
- 디지털 트윈 내에서 실시간 기계 데이터 모니터링 및 유지보수
- 셀프 온보딩 및 원격 교육(특히 위험 및 제한 구역) 강화 및 SeAH의 대규모 시설 네트워크 간의 협업 촉진
- 산업 안전보건 규정 준수를 위한 작업 현장 조건 및 프로토콜 문서화
세아창원특수강(SeAH CSS)은 1966년 설립된 항공 방산 및 항공 우주 산업에 사용되는 첨단 산업 철강재 및 고부가가치 특수 합금을 생산하는 전문 기업입니다.
SeAH는 엔지니어가 현장을 직접 방문하지 않고도 실시간 설비 성능과 같은 정보를 활용할 수 있도록 디지털 세상에 디지털 공장을 구현하는 것을 목표로 합니다.
획기적인 디지털 트랜스포메이션을 위한 길고 어려운 여정
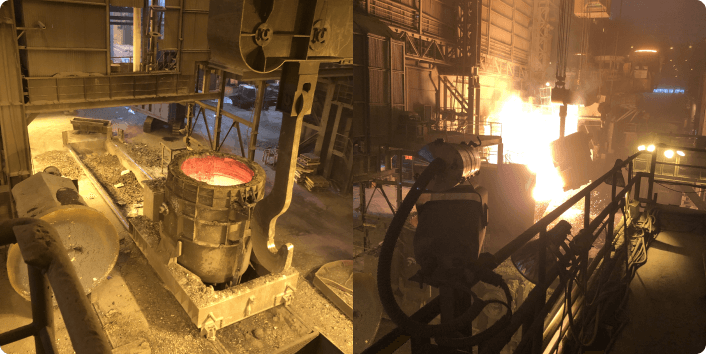
세아창원특수강(SeAH CSS)은 1966년 설립된 항공 방산 및 항공 우주 산업에 사용되는 첨단 산업 철강재 및 고부가가치 특수 합금을 생산하는 전문기업입니다. SeAH는 특수강 업계의 선두주자로서 이미 오래전부터 조직 전반에 걸쳐 디지털 트랜스포메이션을 추진해왔습니다.
세아창원특수강에서는 9개의 공장을 가동 중이며 그중 가장 작은 공장의 규모는 23,500m²입니다. 각 생산 공장마다 평균 4개의 생산 라인과 고도의 전문 설비가 가동되고 있어 생산 지연을 방지하려면 공장 직원이 면밀하게 유지보수하고 모니터링해야 합니다. 한 시설을 검사하기 위해서는 수개월에 걸쳐 최대 7,000장의 사진과 동영상을 손수 수집해야 합니다. 이를 정리하여 보고하는 단계까지 많은 시간이 소요되며, 이러한 사진은 보고 후에는 쓸모없는 데이터가 되어버립니다.
엔지니어가 수동으로 기계를 점검하는데 있어 안전에 대한 리스크가 높다는 문제도 있었습니다. 제강 공정은 극고온 환경에서 이루어지기 때문에 엔지니어가 점검을 하는 동안 고통이 수반될 수 밖에 없었습니다. 또한 한 공장에서 가동되는 기계가 30~40대 정도로, 기계가 가동되는 중에 덮개를 들어올릴 수 없었기 때문에 기계가 완전히 멈추기 전에는 내부 조건을 샘플링할 수 없다는 어려움이 있었습니다.
세아창원특수강은 보다 안전하고 효율적으로 설비를 모니터링하고 유지보수하기 위해 물리적 세계의 상황과 조건을 가상 세계에 구현하고자 했습니다. 채민석 상무/R&D소장은 CAD를 포함하여 공장을 가상 버전으로 복제하기 위해 다양한 솔루션을 사용해보았습니다. 공장 하나를 디지털 트윈으로 설계하는 데만 총 8명의 직원이 투입됐고, 완성까지는 무려 7개월이 소요되었습니다. 7개월에 걸쳐 완성한 3D 가상 공간은 8분짜리 비디오 클립으로 사실상 사용이 어려웠습니다. 원래는 디지털 트윈에 실시간 데이터 피드를 통합하려고 했지만, 이를 달성하지 못했습니다.
또한 SeAH는 자체 개발 플랫폼인 Data Forge에서 프로세스 자동화를 이루기 위해 기계 내부에 로봇 암과 센서를 설치해 왔습니다. 하지만 Data Forge와 가상 세계에 구현한 디지털 공장을 연계하는데 실패하면서 디지털 트랜스포메이션 계획에 큰 변수가 생겼습니다.
디지털 트윈을 빠르고 쉽게 구현하는 방법
SeAH와 Beamo는 소형 압연(RSB) 기계에 디지털 트윈을 구현하기 위한 개념 검증(POC)에 돌입했습니다. 세아창원특수강은 Beamo를 사용하여 넓은 공장 내부를 빠르게 360뷰로 구현하고, 리얼타임 모니터링 시스템을 구축했습니다. 이제 점검자들은 어둡고 접근하기 어려운 복도와 지하, 그리고 중장비 내부까지 Beamo를 활용해 캡쳐할 수 있게 되었고, 언제 어디서든 디지털 트윈 플랫폼 내에서 기계 내부의 모습을 볼 수 있게 되었습니다.
고객사의 엔지니어들은 Beamo를 테스트해본 후 타 솔루션 대비 매우 빠른 시간 안에 디지털 트윈이 구현되는 속도에 가장 놀랐습니다. "기존 솔루션은 수개월이나 걸렸었는데, Beamo를 사용했을 땐 불과 몇시간만에 디지털 트윈을 구현할 수 있었습니다. 시간이 크게 단축됐음에도 불구하고 결과물은 매우 뛰어났습니다."
또한 어두운 공장 내부 조건을 극복하고자 Beamo는 사용자가 캡처 시 360도 사진을 미리 보고, 필요에 따라 Beamo 앱에서 카메라 설정(ISO 감도, HDR, 셔터 속도 등)을 수정할 수 있는 새로운 기능도 추가했습니다.
360뷰로 구축이 완료된 디지털 트윈 내에서 태그 기능을 통해 안전 수칙 및 교육 자료 등을 업로드하여 직원들의 안전 관리가 가능해졌으며, 압연 기계의 센서 데이터를 통합하여 엔지니어들이 공간 정보를 바탕으로 몰입형 모니터링이 가능해졌습니다.
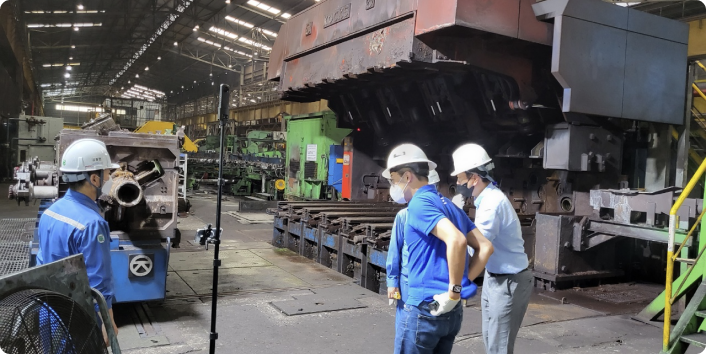
Beamo는 SeAH의 Data Forge와 쉽게 통합되어 태그 기능을 통해 RSB 데이터 차트를 디스플레이합니다. 이제 엔지니어는 현장에 직접 방문할 필요없이, 사무실에서 문제를 보고받고 디지털 트윈에서 상황을 파악할 수 있습니다.
확장을 위한 준비
이제 엔지니어는 현장을 직접 방문하지 않아도 디지털 트윈 내에서 실시간 데이터를 모니터링할 수 있어 원격으로 다양한 정보를 수집하고 활용할 수 있게 되었습니다. 실시간 기계 모니터링을 바탕으로 특정 구역이나 장비에 문제가 발생했을 시 디지털 트윈 내에서 즉각적으로 문제의 위치를 파악하여 조치를 취할 수 있게 되었습니다.
또한 세아는 직원들의 안전 교육을 디지털화하는데도 디지털 트윈을 활용했습니다. 넓고 복잡한 공장 특성상 공장 내부 전체를 돌아다니며 직원들을 온보딩하는 것이 쉽지 않았으나, Beamo 도입 후에는 디지털 트윈 플랫폼 내에서 직원들이 스스로 공장 내부를 가상으로 경험할 수 있게 되어 셀프 온보딩이 가능해졌습니다. 또한 위험한 장비가 많고 제한 구역이 많은 공장에 대한 직원들의 정기적인 안전 교육에도 활용되었습니다.
쉬운 캡처 방법과 빠른 후처리 속도, 그리고 비용 효율적인 솔루션 덕분에 세아는 23,500m² 규모의 공장을 단기간에 고품질로 디지털화했으며, SeAH CSS의 남은 9개 공장(각 공장당 30~40대 기계 보유) 및 그 외의 3개 현장까지 확장하여 솔루션을 적용할 예정입니다.