鉄鋼工場におけるDXのためのユースケース:SeAH昌原特殊鋼(SeAH CSS)
- 迅速で簡単、かつ費用対効果の高いソリューションを活用し、9つの工場とさらに3つの拠点に配備を拡大予定
- リアルタイムな機械データのモニタリングとメンテナンス
- シームレスなセルフ・オンボーディングとリモート・トレーニングを容易にし、特に危険区域や制限区域に関する教育の強化
- SeAHの広範な施設ネットワーク全体のコラボレーションを促進
- 安全衛生規則を遵守のための作業現場の状況やプロトコルの文書化
同社は1966年に設立された専門企業で、航空宇宙、防衛、航空産業向けの先端産業用鋼材と高価値特殊合金を生産しています。
スマートファクトリーの実現を目指しており、エンジニアが直接現場に行かなくても、設備の性能などのリアルタイム情報にアクセスできるようにしたい。
完全なデジタル変革に向けた長く険しい道のり
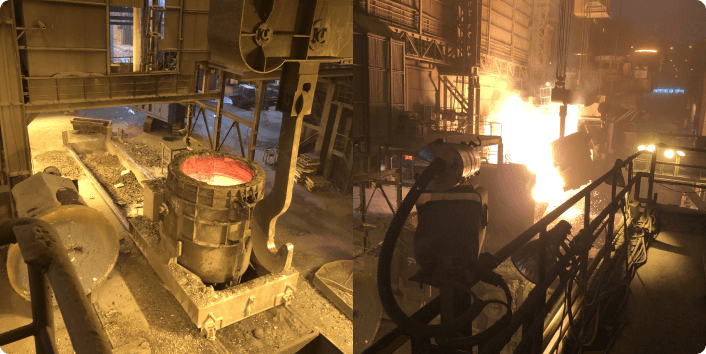
同社は1966年に設立された、航空宇宙・防衛産業向けの先進工業用鋼と高価値特殊合金を生産する専門企業です。特殊鋼業界のリーディングカンパニーとして、長年にわたり組織全体のデジタル変革を推進してきました。9つの工場を運営しており、最も小さい工場でも23,500m²の広さを持ち、各工場では平均4つの生産ラインと高度な設備が使用されています。生産の遅れを防ぐためには、工場の担当者による入念なメンテナンスと監視が欠かせません。ひとつの施設を検査するには、数ヶ月かけて手作業で7,000枚もの写真やビデオを集める必要があります。時間のかかる作業は整理や報告にも及び、収集したデータは報告後に使えなくなります。
さらに、手作業による機械の検査は、特に製鋼工程の過酷な条件下では安全上のリスクが伴います。ひとつの工場で30~40台の機械が同時に稼動しているため、エンジニアは稼動中にカバーを持ち上げることができず、機械を止めずに内部の状態をサンプリングすることができませんでした。
同社は、より安全で効率的な設備の監視とメンテナンスを目指して、物理世界の条件と状況を仮想空間に実装しようとしました。崔敏錫(チェ・ミンソク)取締役副社長兼研究開発部長は、工場をバーチャルに再現するためにCADなどさまざまなソリューションを検討しましたが、1つの工場のデジタルツインを作成するために8人の従業員が参加し、7カ月の時間を要しました。7ヶ月かけて完成した3Dバーチャル空間は8分間のビデオであり、リアルタイムのデータフィードをデジタルツインに統合することに成功しませんでした。その結果、効果的に使用することが困難であることが判明しました。
さらに、同社はロボットアームや機械内のセンサーを使用してプロセスを自動化する社内プラットフォーム「Data Forge」をデジタル複製された工場に接続することに苦労し、デジタル変革計画が大幅に後退する事態に直面しました。
デジタル・ツインをより迅速かつ簡単に作成する方法
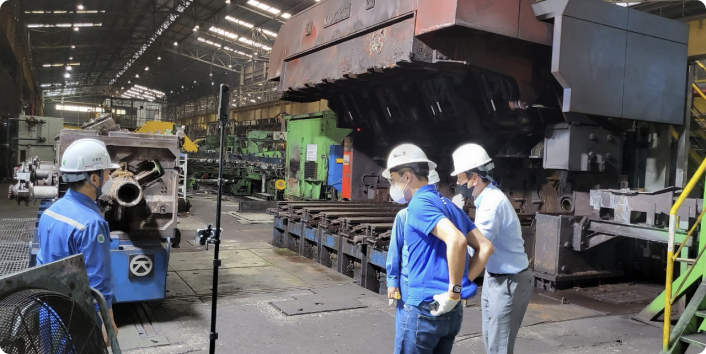
SeAHとBeamoは、小型圧延機(RSB)にデジタルツインを導入するための概念実証(POC)に着手しました。Beamoを活用することで、SeAH Changwon Special Steel社は、広大な工場の360度ビューを迅速に導入し、リアルタイムの監視システムを確立しました。現在、検査員はBeamoを使用して、暗い廊下、地下空間、重機の内部などの困難な場所を撮影し、いつでもどこからでもデジタルツインプラットフォーム内で機械の内部を見ることができます。
SeAH社のエンジニアは、Beamoがデジタルツインの実装を可能にしたスピードに感銘を受けました。「以前のソリューションでは数カ月を要したのに対し、Beamoではわずか数時間でデジタルツインを作成でき、時間を大幅に短縮しながら優れた結果を得ることができました。」
暗い工場環境の課題を克服するため、Beamoは、ユーザーが撮影前に360度写真をプレビューできる新機能を導入しました。さらに、ユーザーは必要に応じてBeamoアプリからカメラの設定(ISO感度、HDR、シャッタースピードなど)を変更することができます。
360度ビューのデジタルツインが完成すると、SeAH社はタグ機能を活用して安全ガイドラインや教材をアップロードし、従業員の安全管理を促進しました。圧延機のセンサーデータを統合することで、エンジニアは空間データに基づく没入型情報をモニターできるようになりました。
拡大への準備
これにより、エンジニアは現場に行かなくても、デジタルツイン内のリアルタイムデータをリモートで監視できるようになりましたし、さまざまな情報をリモートで収集・活用できるようになりました。リアルタイムで機械をモニタリングすることで、デジタルツイン内の特定のエリアや機器の問題を即座に特定し、迅速な対応が可能になりました。
SeAHはまた、デジタルツインを使用して従業員の安全トレーニングをデジタル化しました。広大で複雑な施設で従業員をオンボーディングするのは困難でしたが、Beamoの導入後、従業員はデジタルツインプラットフォーム内で工場をバーチャルに体験できるようになり、セルフオンボーディングが容易になりました。さらに、危険な機器や制限区域が多い工場で、従業員の定期的な安全教育にも活用されました。
簡単なキャプチャ方法、迅速な後処理、費用対効果の高いソリューションにより、SeAH社は23,500m²の工場を短期間で効率的にデジタル化しました。同社は、このソリューションを残りの9つのSeAH CSS工場(各工場には30~40台の機械がある)と、さらに3つの拠点に拡大する予定です。