At 3i Inc, we create products that enable people to go beyond their limits. We want to help make people’s lives better. That is how Beamo was created. Beamo is an enterprise-grade digital twin solution that’s easy, fast, and scalable, designed for mission-critical facilities. These mission-critical facilities can include smart factories, data centers, construction sites, demolition sites, complex urban offices, and so on. Last year, 3i worked with SeAH CSS to digitize one of their factories. The PoC project was a success, though we met a few obstacles that ultimately became valuable lessons for us, too.
Among the various lessons we learned, in this particular article, we want to mostly share how we developed Beamo to help users take good 360° photos in any situation. As mentioned in an earlier article, Beamo has the technology to make 3D Digital Twins using 360° photography. So, like any successful dish with one main star ingredient, the quality of the digital twin output depends heavily upon the quality of the 360° photos taken.
It’s easy to make a digital twin of a simple space like a warehouse or an office with good enough lighting conditions. But with specialized facilities, more complexity usually comes with the area. For example, special steel factories and semiconductor factories have a more complex process and production phase than say a sole steel factory or a simple pencil or paper factory. This complexity extends beyond just the process and production line, which are directly related to manufacturing, to also their monitoring systems, maintenance systems, and other non-direct, sub-management systems.
Because these special facilities come with their own sets of strict requirements and idiosyncrasies, they are very likely to have abnormal qualities that make capturing more challenging. For the case of SeAH CSS, their factory had a complex lighting system that created an imbalance in the resulting 360° shots. A single point of capture would reveal different lighting conditions from multiple directions, making the shot strange and unnatural.
Another problem was the motor of a heavy industrial machine causing constant floor vibrations resulting in blurry 360° shots. These various situational factors are often present in special facilities and can often be a hindrance to taking good quality photos for digital twin creation.
Lights, camera, Beamo!
Our main objective for users is to ensure a fast and easy solution for digital creation. With that in mind, we knew we had to ramp up our 360° photo capturing process, while still leveraging on readily available off-the-shelf 360° cameras and consumer smartphones.
After much R&D, we equipped Beamo with the capacity to handle any situational abnormalities by enabling full controllability of the synced camera system. We added new developments to the Beamo App to directly manipulate its synced 360° camera and to also automatically tune its own settings, like ISO, Shutter speed, aperture, HDR, and EV, for the user’s ease of capture. It was not a straightforward process, to say the least since all these camera tools relate and interact differently with each other. Getting the right mix plays heavily into producing quality images with the right exposure.
In the case that the automatic 360° camera settings cannot perform well due to extreme environmental challenges, users can manually control the camera tools, simultaneously check the live stream of the synced 360° camera, and adjust accordingly.
But the reality is that most of the users would not be as familiar with 360° camera settings and tools, so we also decided to provide semi-auto mode. Semi-auto mode allows users to control just one major factor that is most relevant for the environment (eg. aperture for dimly lit areas) and the system automatically optimizes all the other factors.
Images taken before and after the Beamo update
The perfect handy tool
The next piece of the problem was finding the best method for capturing. Different situations and environmental factors call for different modes of capture (ex. tripod for stability, monopod for reach and flexibility, drone for large open areas.) So we wanted the design to be (1) modular so that it can transform into a tripod, monopod, etc. as needed for the situation, and (2) as compact and efficient as possible.
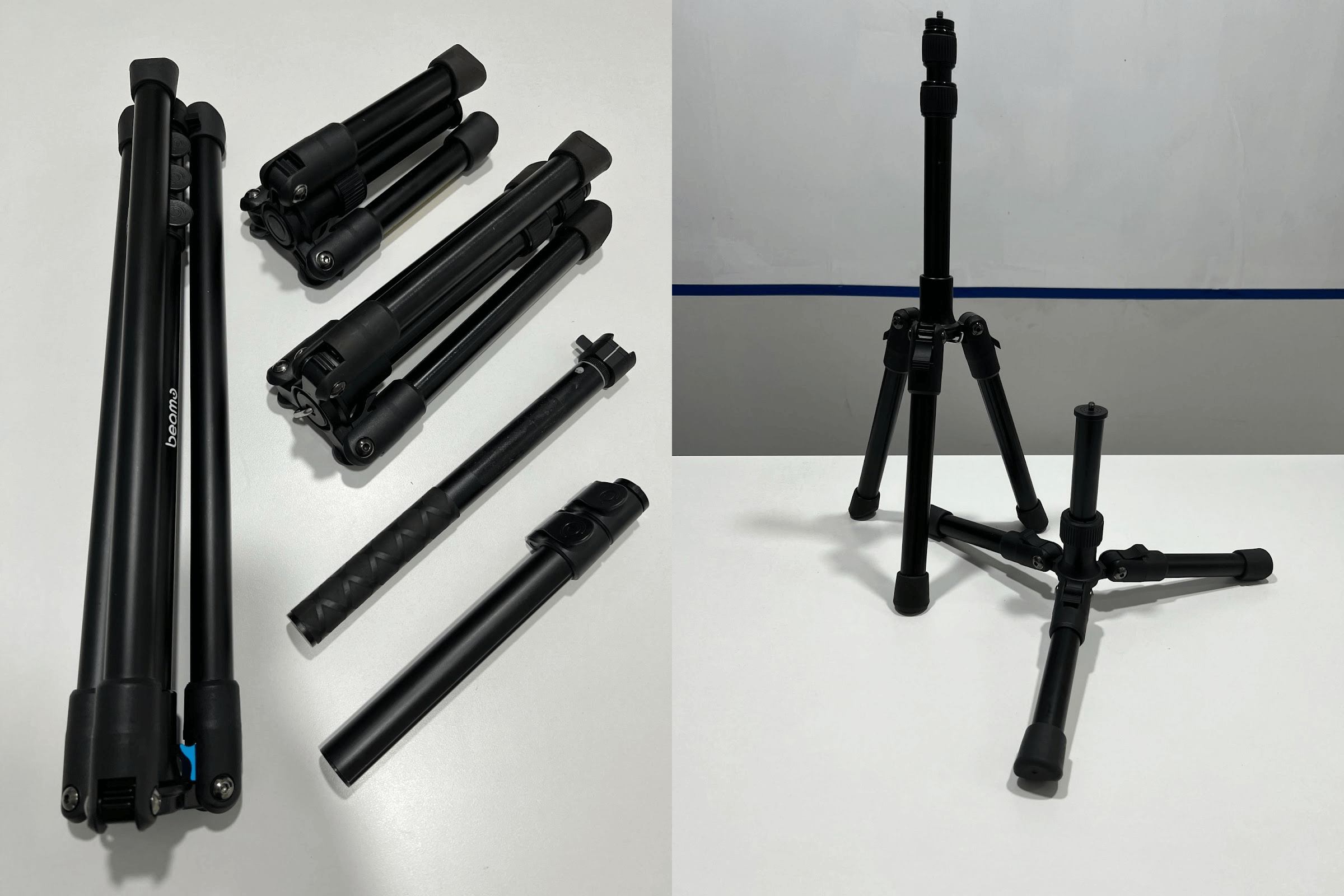
Left: Variations of Starter Kit: Tripod, Mini Pod 1, Mini Pod 2, Monopod 1, Monopod 2
Right: Variation of small Starter Kit Tripods
For this, we basically designed our tripod to be as short and small as possible. We designed a tripod complete with all the essential features while cutting down on the unnecessary dimension requirements. We also developed the monopod use case for capturing narrow, hard-to-reach places like underground entrances, interiors of large machinery, floor and ceiling plenums, etc. Lastly, with the auto-leveling feature added, any user can just start capturing any site, no matter the level of difficulty. No expertise required.
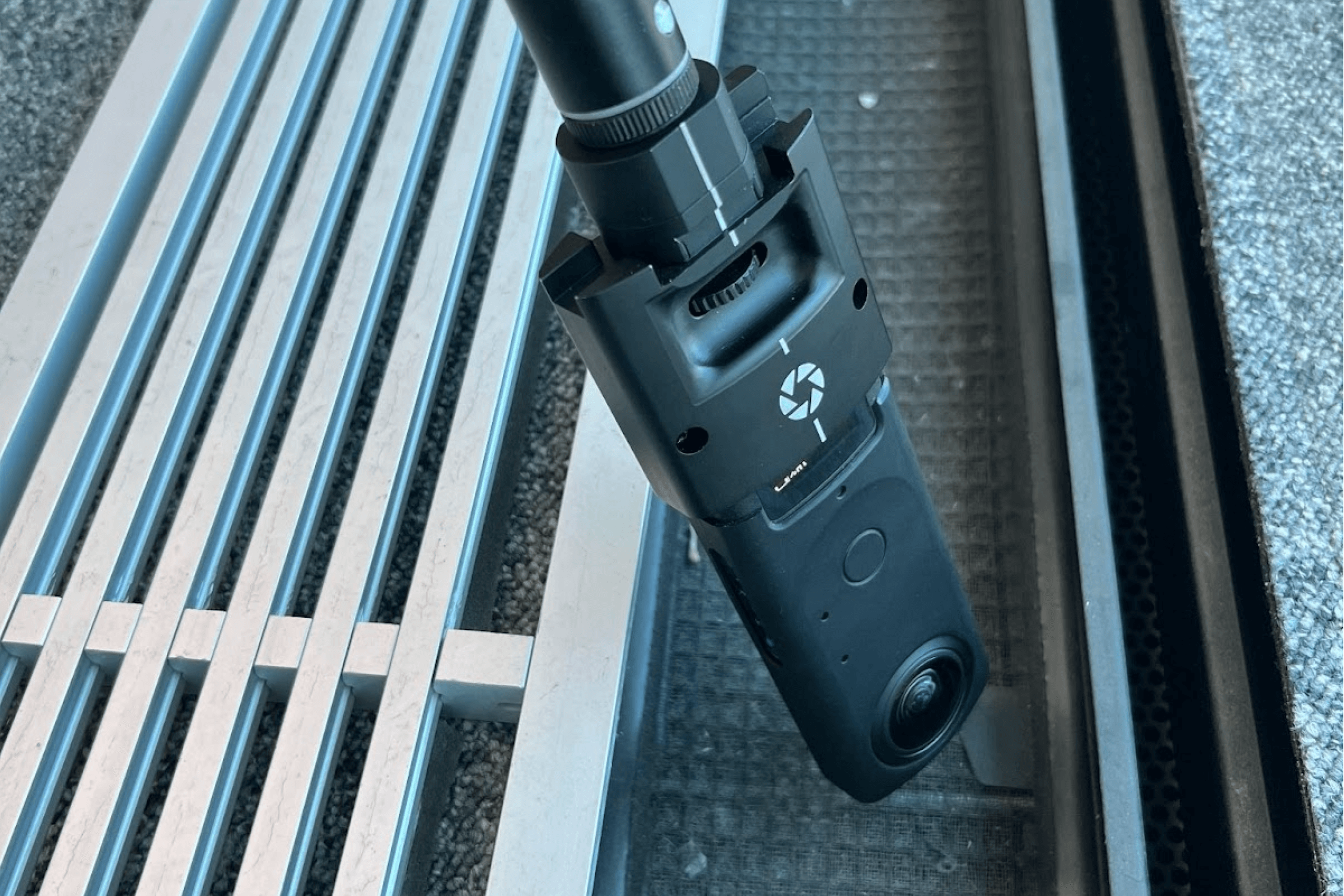
Beamo's auto-leveling feature allows users to take 360° shots at any angle.
Capture everything anywhere
These new developments solved how just about any user can start capturing good 360° photos to produce crystal clear digital twins for the challenging environments of mission-critical facilities. After all, digital twins have the potential to be the single source of truth. It is important that these digital twins are accurate and have high fidelity.
I believe Beamo is now capable of capturing the complete picture of various types of mission-critical facilities. A complete digital twin means not just the exposed, common floor areas that you normally see but also areas that are harder to access and reach such as the basements, ceilings, machine interiors, spaces between underground water pipelines and upper moving tracking lines, etc. And as we continue to meet new obstacles and improve our solution, Beamo will be capable of capturing any extreme environment, even a volcano!
Written by Taeyeong Moon, product manager, Beamo
Edited by Riana Chua